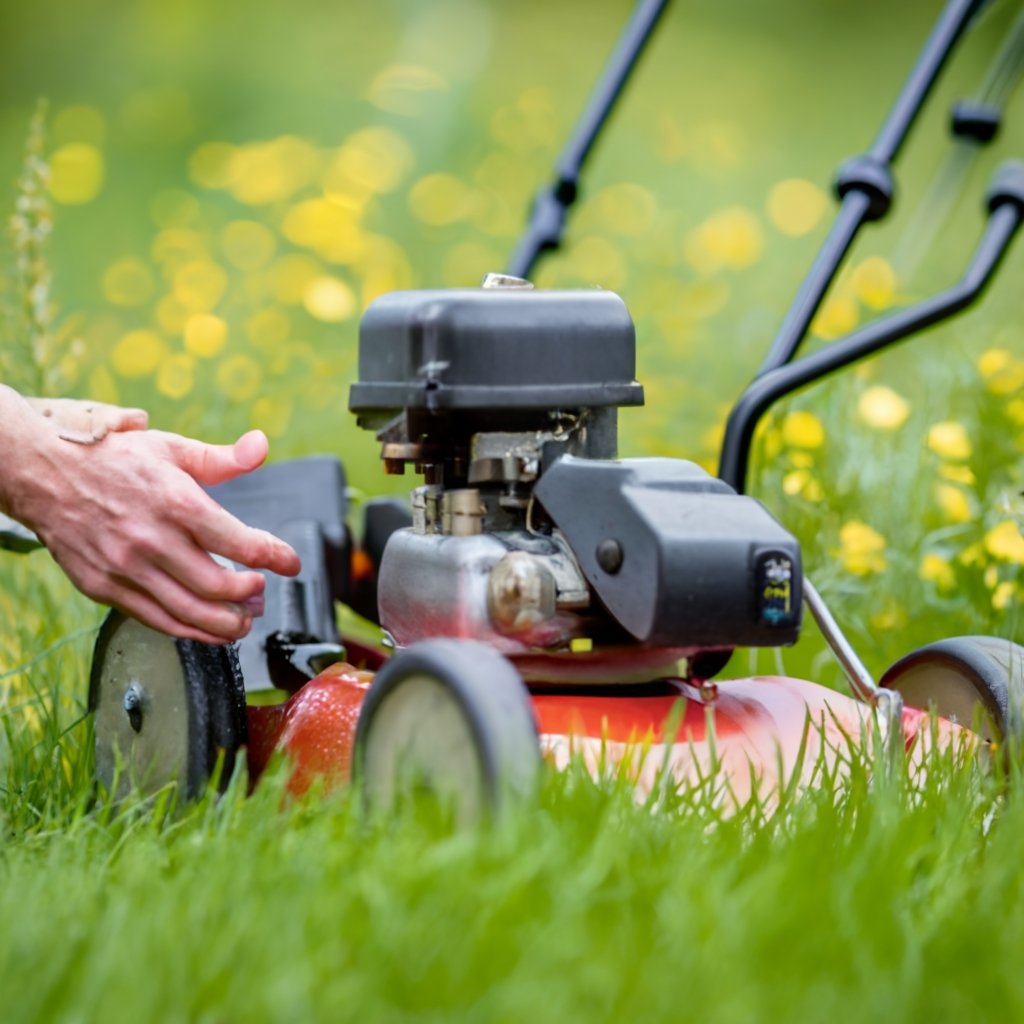
Is your lawn mower dead in its tracks when you turn the key? Before calling the repair shop, try jump starting the solenoid first! Diagnosing and jumping a faulty solenoid is an easy DIY fix to breathe life back into your dead mower and avoid a hefty shop bill. Learn how to safely hotwire and test the solenoid in a few simple steps. We’ll walk through identifying common symptoms, isolating the solenoid as the culprit, jumper cable setup, pro replacement tips, and more starter system secrets. Don’t pay a premium for a basic repair – our complete solenoid troubleshooting guide will get your mower roaring again. Let’s fire it up!
How To Jump Solenoid On Lawn Mower – The Complete Guide
What is a Solenoid on a Lawn Mower?
The solenoid on a lawn mower is a critical component that allows the engine to start up. It is essentially an electromagnet that, when energized, pushes the starter drive forward to engage the flywheel and crank the engine. Without a properly functioning solenoid, you will simply hear a “click” or no noise at all when turning the key, but the engine will not crank and start.
The solenoid is wired into the lawn mower’s ignition circuit and activated when the key is turned. As current flows into the solenoid, its electromagnet builds up enough magnetic force to overcome the spring pressure that holds the starter drive in the disengaged position. The starter drive is pushed forward, meshing the gear on its shaft with the flywheel gear to turn over the engine. Once the engine starts and the key is released, the current flow stops, the magnetic field collapses, and the spring retracts the starter drive back to the disengaged position.
So in summary, the humble little solenoid performs the crucial task of physically engaging the starter motor pinion gear with the engine flywheel to get the mower running. Without it, you’d be stuck pulling on the recoil rope starter like the old days!
Here are some key points on why the solenoid is indispensable for starting your mower’s engine:
- Converts Electrical Signal to Mechanical Movement: The solenoid receives a small electric current from the battery and ignition switch. It then uses electromagnetic force to mechanically shift the starter drive gear to turn over the engine.
- Provides Leverage for Starter Motor: The solenoid plunger pushes the small starter drive gear forward with considerable mechanical force. This allows a high gear reduction ratio to crank the engine.
- Disengages Starter After Ignition: The solenoid retracts the starter gear from the flywheel automatically once the mower starts, preventing damage.
- Makes Starting Effortless: Starting the mower involves simply turning a key rather than strenuous manual recoiling. The solenoid does all the heavy lifting!
- Longer Starter Life: The solenoid bears the brute force of cranking the engine, protecting the starter motor from excessive wear and tear.
So in effect, the solenoid acts as a powerful robotic arm that does the grunt work of starting your mower safely and easily at the turn of a key. It’s a compact component that plays an outsized role in allowing convenient, push-button starting of your mower.
Signs Your Lawn Mower Solenoid is Bad
So your lawn mower won’t start or is acting up when you try to start it? There’s a good chance the solenoid is to blame. Here are the most common signs that indicate your mower’s solenoid is bad and needs attention:
The Engine Won’t Turn Over
This is the clearest symptom that the starter solenoid is faulty. When you insert the key and turn it, you expect the satisfying sound of the engine cranking and coming to life. But with a bad solenoid, you’ll turn the key and get nothing – no sound, no motion, nothing.
It’s as if the ignition switch is disconnected from the starter. Because that’s exactly what a malfunctioning solenoid does – it fails to engage the starter motor to turn over the engine. The wiring may be fine and battery charged, but no juice is reaching the starter to crank the motor because the solenoid isn’t doing its job.
A Rapid Clicking Sound When Trying to Start
If your mower makes a quick clicking or rapid ticking noise when you turn the ignition key, it points to trouble with the solenoid.
This clicking comes from the solenoid repeatedly engaging and disengaging the starter motor gear very quickly, but not properly engaging it long enough to start the mower. It’s trying to work but unable to sustain the contact and force needed to effectively turn over the engine.
The clicking indicates a problem with the solenoid coil that prevents it from generating the magnetic force required to drive the starter gear into the flywheel. It’s trying hard but lacking the power to fully do its job. Just not enough oomph in its electromagnet!
The Engine Cranks But Doesn’t Start
In some cases, the solenoid seems to be working fine as the engine cranks when the key is turned. But then it fails to actually fire up and run.
This can point to a solenoid that is on its way out but hasn’t completely died yet. A weakening solenoid may be able to engage the starter motor, but not deliver enough sustained power to fully turn over the engine for ignition.
So the engine sputters, almost catches, then doesn’t start up. It exhibits an anemic cranking that shows the solenoid isn’t quite up to snuff. Basically a solenoid with diminished capacity on its way to conking out.
The Mower Starts Then Stalls Out
Here’s an all too familiar scenario – your mower starts fine, but then dies shortly after. Or it starts intermittent and runs rough, sputtering for a bit before stalling out.
More often than not, this points to a solenoid with bad contacts that is losing power intermittently once the engine heats up and expands. When cool, it engages fine to start the mower. But expanding metal from heat causes a bad connection, making the solenoid cut in and out.
It can also indicate dirt, debris, or corrosion on the solenoid contacts preventing a solid connection. Either way, an engine that starts then stalls repeatedly or runs rough is oftentimes a precursor to solenoid failure.
So in summary, it you experience no cranking, rapid clicking, bad cranking, or intermittent stalling – the common culprit is likely a solenoid problem. When you see these symptoms, it’s definitely time to start troubleshooting or replacing that little starter relay that has such an important big job.
How to Test if the Solenoid is Bad
Experiencing symptoms of a faulty solenoid? Before condemning it to the scrap heap, some simple tests can confirm if the solenoid is truly malfunctioning or if another issue is to blame. Here are three easy ways to test and diagnose problems with your mower’s solenoid:
Use a Multimeter to Check Continuity
Checking for electrical continuity through the solenoid is one of the best ways to test its operation. You’ll need a multimeter set to ohms for this.
First, disconnect the battery and solenoid wiring harness. Then, touch the multimeter probes to the large terminal studs on either end of the solenoid (where the battery cables attach). The solenoid should show continuity – very low resistance, almost zero ohms.
If you get a high resistance reading, it indicates a break in the contacts inside the solenoid, meaning replacement is needed. If the meter shows continuity, the solenoid coil and internal contacts are likely fine.
Listen for Clicking When Trying to Start
If the mower makes a rapid clicking sound when the key is turned but won’t start, focus your diagnosis on the solenoid.
With the battery connected, turn the key and listen closely to the solenoid. A distinct, audible click when the key is switched indicates the plunger is engaging but immediately retracting – not able to hold the contact to crank the engine.
No click at all points to an electrical issue before the solenoid. But a pronounced click signifies erratic solenoid operation typically from a weak or damaged coil.
Check for Power at the Solenoid
Use a test light or multimeter at the solenoid wiring connector to check if power is arriving when the key is turned. Probe the small activation wire that energizes the solenoid.
If the test light illuminates or the meter shows 12 volts, you know power is getting to the solenoid. But if there is no power reading, there is likely an open fuse, bad ignition switch, or wiring issue that needs to be addressed first.
This quick power check can prevent wasting time diagnosing a solenoid that isn’t bad but simply isn’t receiving current. Focus on the wiring components leading to the solenoid.
In summary, listening for click, checking continuity, and power testing at the solenoid connector enables isolating or ruling out the solenoid as the culprit. Don’t just guess – take a few minutes to definitively test and conclude if that little starter relay is the reason your mower won’t start.
How to Jump a Lawn Mower Solenoid
So you’ve determined the solenoid is likely the culprit for your mower not starting. Before running out to buy a new one, you can try jumping the solenoid to potentially revive it and confirm that’s the issue. With a few basic tools and proper precautions, here is how to safely jump a lawn mower solenoid to test its operation:
Gather the Proper Supplies
You’ll need the following tools and items on hand to jump the solenoid:
- Jumper cables – Use heavy duty ones with adequate length to connect from the battery to solenoid.
- Insulated pliers – To grip and remove connectors and wiring.
- Safety glasses – For eye protection from sparks or battery acid.
- Work gloves – Insulated gloves rated for electrical work.
- Rags – For cleaning and grip when handling oily parts.
- Headlamp or shop light – To illuminate the engine area for visibility.
- Solenoid specifications – Reference voltage, connector type, wiring colors.
Gather everything beforehand so you have it ready to go for this temporary solenoid hotwire procedure.
Identify the Solenoid on Your Mower
On most mowers, the starter solenoid is a cylindrical or rectangular component 3-4 inches long mounted directly on top of the starter motor housing.
Trace the positive battery cable to find where it connects to one large post on the solenoid. The other large post goes to the starter motor. A smaller terminal will have the activation wire from the ignition key switch.
If you’re unsure of the solenoid location and wiring, consult your mower’s repair manual for the specific model. Correctly identifying components is crucial for proper jumper cable setup.
Safely Disconnect the Battery
Before doing any work around the electrical system, always disconnect the negative battery cable first to cut power. Remove the positive cable next. Tuck them away from any metal contacts.
Disconnecting the battery prevents accidental shocked or sparks from live current during the solenoid testing process. Safety first!
Detach the Solenoid Wiring Connector
Locate the wiring harness leading from the ignition switch to the small activation post on the solenoid. This is held by a nut or clip – use pliers to detach it and set it safely aside.
This disconnects the solenoid from the mower’s ignition circuit so it can be independently powered for standalone testing.
Connect Jumper Cables to Solenoid Terminals
Attach one jumper cable clamp directly to the positive battery post on the solenoid. Connect the other clamp to the spade terminal where the main starter wire attaches.
This will allow battery power to flow directly through the solenoid activation path when energized, bypassing any external wiring issues.
Momentarily Power the Solenoid
Have a helper turn the ignition key to allow battery current to flow through the solenoid. Do NOT crank the starter yet. Listen for a distinct audible click.
If no click, the solenoid is likely bad. A click indicates it’s engaging. Proceed to crank the engine over as described in the next step.
Activate Starter to Test Solenoid
With cables secured on the posts, have your assistant turn the ignition key to the start position. This should crank the starter motor, allowing the solenoid to engage and spin the engine.
If the engine turns over normally, the solenoid is likely okay and the problem lies with the starter or ignition wiring. If it clicks but won’t crank, the solenoid needs replacing.
Reconnect Everything if Solenoid Checks Good
If it passed the jump test by spinning the motor, turn the mower off. Remove the jumper cables and reconnect the battery cables and solenoid harness connector.
Try starting the mower normally by turning the key. If it works, you’ve successfully revived the solenoid and saved some repair cost.
Replace Solenoid if Found Defective
If the solenoid failed to engage the starter and turn over the engine when jumped, it will need replacing. Turn off the key and remove jumper cables.
Match a new solenoid to your mower’s specifications. Install it using the reverse process of the steps above. With the fresh solenoid installed, the mower should be ready to start reliably again.
Jumping the solenoid as described is an effective way to isolate whether the solenoid itself is bad or if starter issues are to blame. Take proper safety measures, and the procedure can confirm if solenoid replacement is required to get your mower running again.
Solenoid Repair and Replacement
Jumping the solenoid is a handy temporary fix, but often a failing solenoid will need more substantial repair or full replacement to get long-term reliable operation again. Here are tips on cleaning, replacing, and troubleshooting stubborn solenoid issues:
Attempt Cleaning and Testing First
Before replacing, consider disassembling and cleaning the solenoid contacts with electrical contact cleaner spray. Hardened grease, dirt, and corrosion on the contacts can cause connection issues.
Use coarse sandpaper or a small file to gently buff the contact surfaces. Reassemble and conduct solenoid testing steps to see if operation improves.
Exercising the plunger and working the contacts helps diminish carbon buildup. Frequently cycling the solenoid during cleaning can extend its life.
Replace the Solenoid If Needed
If cleaning efforts don’t restore proper solenoid function, replacement will be required. Make sure to get an exact matching new or OEM solenoid made specifically for your mower model.
When installing the new solenoid, use dielectric grease on the electrical terminals to prevent corrosion. Properly torque wiring connections to avoid loose contacts. Bench test operation before reinstalling.
Follow mower manufacturer instructions to safely replace the solenoid. Taking your time will get the re-wiring right the first time.
Still Won’t Start? Further Troubleshoot Ignition System
If replacing the solenoid and jumper testing checks out fine, but the mower still won’t start, the underlying problem likely lies elsewhere:
- Starter – If solenoid clicks but starter doesn’t spin, the motor is probably bad.
- Battery – Weak cranking or no lights often indicates insufficient charge and power.
- Ignition switch – Old or dirty switches can have open contacts causing no spark.
- Wiring – Fraying, loose connectors, or cut wires will lead to failure.
Carefully inspect components in the ignition and starting system. Check for voltage drop and resistance across wires and terminals. Isolate the specific area of the circuit that is compromised.
With some diligence and voltage measurements, the source of an ongoing no start issue can be narrowed down. The solenoid may turn out to be an innocent bystander!
Proper solenoid repair and replacement, along with targeted electrical diagnostics, will ultimately solve elusive starting problems. Just don’t assume the solenoid is bad without confirming – be thorough in your troubleshooting.
Safety Tips for Jumping a Solenoid
When hotwiring a lawn mower solenoid, safety should always be the top priority. Jumper cables are handling battery current, so caution is required. Follow these tips to prevent electrical shocks, sparks, and other hazards when testing a solenoid:
Use Protective Gear
- Wear ANSI-approved safety glasses to shield your eyes from sparks or battery acid.
- Electrical gloves rated for voltage work will insulate your hands from shocks.
- Long sleeves and pants prevent exposed skin from touching live terminals.
- Close-toed shoes protect your feet from falling tools or large jumper clamps.
- Remove jewelry, ties, scarves that could catch on spinning pulleys or mower blades.
Proper protective apparel reduces the risks when testing around live electrical connections. Don’t neglect safety gear.
Ensure Blades Are Disengaged
Before starting any solenoid testing, verify the mower blade lever is in the disengaged position. This prevents the blades from spinning unexpectedly if the engine starts.
Also disconnect the spark plug wire(s) to prevent accidental ignition before cranking the motor over. Eliminate all hazards before beginning.
Connect Cables Carefully
- Keep cables away from moving parts like belts, pulleys and blades that could snag or cut into exposed wires.
- Avoid touching both jumper clamp contacts simultaneously to prevent forming a circuit through your body.
- Connect cables with insulating pliers or gloves on to limit shock hazard.
- Check for frayed wire insulation and damaged clamps before using old jumper cables.
- Confirm polarity – positive cable to positive post, negative to negative metal ground.
Mindfulness when connecting jumper cables prevents painful sparks and shorts. Take it slow.
Secure Cables Properly
- Use pliers to tighten clamps for a snug, secure metal-to-metal connection.
- Route cables away from heat sources, sharp edges, and dangerous pinch points.
- Support cable weight to avoid strain on connections which can work loose.
- Observe cable connections while testing, and stop if they overheat from resistance.
Proper jumper cable positioning reduces the chances of a damaged cable or lost connection during testing.
Reconnect Battery Safely
Before reconnecting battery:
- Ensure cables are removed from solenoid posts to avoid sparks.
- Verify ignition switch is OFF to prevent starter engagement.
- Clean terminals and apply dielectric grease to prevent future corrosion.
- Connect POSITIVE cable to battery first, then NEGATIVE cable last.
- Avoid leaning over battery – make final connection from the side.
Carefully follow the correct procedure when re-attaching battery wires to avoid explosion risk from hydrogen gas buildup.
Adhering to basic electrical safety practices will keep you, your test equipment, and your mower protected when diagnosing solenoid issues. Don’t take shortcuts – safe solenoid testing prevents accidents and injuries!
FAQs About Lawn Mower Solenoids
Let’s review some frequently asked questions and answers about common solenoid issues to expand your working knowledge about this critical mower component:
What if Jumping the Solenoid Doesn’t Work?
If connecting jumper cables directly to the solenoid does not energize the starter motor at all, it likely indicates an internally damaged solenoid that will need replacing.
If the starter cranks slowly or erratically, the solenoid contacts may be worn or corroded. Try cleaning and testing it further before condemning it.
But if jump starting the solenoid yields no response from the starter, the solenoid is likely bad and will need to be replaced.
How Much Does it Cost to Replace a Solenoid?
The cost for a new lawn mower solenoid can range from $20-60 depending on the specific model. More heavy-duty solenoids for larger riding mowers may cost up to $100.
OEM solenoids from the original manufacturer tend to cost more but provide a quality exact replacement part. Aftermarket generic solenoids can be a cheaper alternative for older mowers.
In most cases, replacing the solenoid yourself will be far cheaper than paying a small engine repair shop $80-150+ for the labor.
Is it OK to Run a Mower with a Bad Solenoid?
It is generally not recommended to continually use a mower with a malfunctioning solenoid. As the solenoid further deteriorates, it can leave you stranded with a non-starting mower.
A faulty solenoid that engage intermittently can also damage the starter motor as it tries to engage with inadequate power. Better to replace it before other issues crop up.
However, you can likely continue using a mower with a slightly weak solenoid for a short period by jump starting it until you can replace it. But repair it promptly.
What Causes a Solenoid to Go Bad?
- Extended use leading to burned, eroded electrical contacts
- Vibration cracking magnet wire windings
- Corrosion buildup on connections
- Carbon and dirt fouling moving parts
- Excessive starter cranking overheating the coil
- Age and weather deterioration
Basically, the solenoid is a mechanical component subject to wear and tear over time. Proper maintenance can maximize its lifespan.
How Can I Prevent Solenoid Failure?
- Keep battery fully charged to avoid overworking solenoid.
- Clean solenoid contacts and apply dielectric grease.
- Check wire connections are clean and tight.
- Avoid excessive and prolonged cranking to start.
- Confirm proper voltage to ignition system.
- Store mower protected from moisture and extremes.
- Consider replacing solenoid proactively after 5-8 years.
With proper care, the solenoid can provide many years of reliable starting. But it’s a maintenance item that needs attention to maximize its service life.
Regular inspection, cleaning, testing, and preemptive replacement if needed will prevent getting stranded with a bad solenoid at the worst time.
Key Takeaways and Summary
Let’s recap the core information about diagnosing and testing lawn mower solenoids:
- The solenoid is the electromagnetic switch that engages the starter to crank the engine when starting.
- Common symptoms of a bad solenoid are the engine not cranking, rapid clicking sounds, weak cranking, and intermittent stalling.
- Jumper cables can be connected directly to the solenoid to provide power and test its operation separate from the mower ignition. This can confirm if the solenoid itself is bad or if other electrical issues are present.
- Exercise caution when jump starting a solenoid – use protective gear, secure cables properly, ensure no blade contact, and connect/disconnect battery correctly.
- A solenoid that is found to be defective via jump testing will need to be replaced with an exact replacement part for reliable restarts.
- Even if the solenoid checks out, persistent no start conditions can be caused by other ignition problems like bad starter, switch, battery or wiring issues.
- Preventative maintenance goes a long way for maximizing solenoid life – keep connections clean, reduce corrosion, avoid over-cranking, and consider proactive replacement after several years of use.
Jumping a solenoid is a handy technique to confirm starter issues on a non-starting mower. Combined with smart maintenance habits, you can get the most life from your mower’s starting solenoid.
Don’t hesitate to refer to this guide when those dreaded no start symptoms arise. And as always, exercise caution when testing around electrical systems to avoid shocks and shorts.
With this knowledge in your toolbelt, you can troubleshoot and revive a balky solenoid to get your mower running again! Here’s to green grass ahead.
Key Takeaways for the Entire Article
- The solenoid is the small but mighty electromechanical switch that engages the starter to crank and start the mower engine.
- Common symptoms of a failing solenoid are the engine not cranking, rapid clicking noises, intermittent operation, and weak cranking.
- Thoroughly test the solenoid by checking continuity, listening for sounds, and verifying power is arriving to isolate it as the problem before replacing.
- Jumper cables can be directly connected to the solenoid posts to provide temporary power to it and bypass any external wiring issues during testing.
- Exercise extreme caution when jumping a solenoid – use insulated tools, wear gloves/glasses, secure cables properly, and disconnect battery correctly.
- If jumping the solenoid confirms it is defective, replace it with an exact OEM part to permanently resolve no start issues.
- Persistent starting problems after solenoid replacement may indicate other ignition faults – thoroughly diagnose starter, battery, switch, and wiring issues.
- Proper preventative maintenance and cleaning extends the service life of the solenoid – but it is a wear item that needs periodic replacement.
- Following safe testing procedures and smart solenoid maintenance practices will allow getting the longest lasting performance from this integral mower component. Frequently Asked Questions
Q: What are the most common symptoms of a bad lawn mower solenoid?
A: The main symptoms are the engine not cranking when trying to start, a rapid clicking sound but failure to start, weak/slow cranking, and the mower starting then stalling intermittently.
Q: How can I test if the solenoid is bad?
A: Use a multimeter to check for continuity, listen for clicking sounds when trying to start, and verify power is getting to the small activation terminal. Jumping the solenoid with cables directly on the posts can also determine if it is engaging properly.
Q: Is it safe to jump start a lawn mower solenoid?
A: Yes, with proper precautions – use insulated tools, disconnect the battery, secure cables away from moving parts, connect polarity correctly, and wear protective gear in case of sparks. Follow all electrical safety practices.
Q: What if jumping the solenoid does not work?
A: If directly powering the solenoid does not crank the starter motor, it indicates internal damage and the need to replace the solenoid. Also rule out a seized engine or damaged starter motor.
Q: How much does a replacement lawn mower solenoid cost?
A: Solenoid prices range from $20-60 for common mower models. OEM exact replacement solenoids cost more than generic aftermarket versions. Professional installation can add $80-150 or more.
Q: If I replace the solenoid, could other issues cause continued starting problems?
A: Yes, weak battery, faulty ignition switch, bad starter motor winding, corroded wiring and connections, or other ignition issues could prevent successful starting even after a solenoid replacement.
Q: How can I extend the life of my mower’s solenoid?
A: Keep connections clean and corrosion-free, avoid over-cranking the starter, proper battery maintenance, protect mower from weather extremes, and consider replacing solenoid proactively every 5-8 years.